В салонах по продаже клинкера, керамогранита и керамической плитки можно увидеть на демонстрационных стендах «батареи» ступеней: натуральных цветов, глазурованных и покрашенных в разные рисунки и цвета на любой вкус с любыми фактурами от совсем нескользящих до антискользящих R13. А вот в действительности, настоящего «клинкера» там практически нет. А где же настоящий клинкер спросите Вы ? Давайте разбираться вместе!Сегодня «клинкером» называют напольную плитку и ступени (фронтальные, угловые) для облицовки крыльца и ступеней то есть, преимущественно для экстерьерной отделки домов, зон мангала, барбекю, лестниц.
Клинкерные ступени и напольная плитка – это материал который производится исключительно из сортов тугоплавких глин. В составе «рецепта» настоящего клинкера только тугоплавкая глина и ничего другого кроме нее в рецепте нет. Обязательным составом рецепта настоящего клинкера является «шамот» - это по сути тот же самый клинкер, который уже прошел обжиг в туннельной печи, но после этого его дробят на специальном оборудовании и добавляют в массу глины до формовки. Шамот необходим для «отощения массы» – т.е. снижения пластичности, он улучшает сушильные характеристики, снижает огневую усадку, облегчает режим обжига (режим нагрева и режим охлаждения), не меняет химический состав шихты (сырья). Кроме того, применение в шихте шамота, важно с точки зрения охраны окружающей среды и создания безотходной технологии производства. Процент шамота, в зависимости от рецептов, может составлять от 5% до 15%. Месторождения тугоплавких глин есть в Европе и России.
Клинкер производится методом ВЕРТИКАЛЬНОЙ экструзии (выдавливания) – такой метод позволяет делать ступень с литым капиносом т.е. носик ступени составляет единое целое с плиткой. Такое изделие прослужит долгие годы и не сломается. При формовании, из экструдера выдавливаются заготовки, соединенные между собой техническими перемычками (ребрами жесткости). Это дает возможность за одну формовку производить больше материала, кроме того – это необходимо для обеспечения устойчивости материала на конвейерной ленте и при последующих этапах работы с ним.
Далее, заготовки по конвейеру направляются на нарезку под определенный размер (режет как правило специальная струна) и после этого материал поступает в сушильные камеры, там заготовки сушатся до 40 часов при температуре от 90 до 98 градусов. После предварительной сушки, заготовки по конвейерной ленте поступают на глазуровку и покраску (если необходимо). Далее, заготовки роботизированными механизмами расставляются специальным образом на вагон в 2-3-4 ряда в высоту и проходят обжиг на вагоне в туннельной печи длинной 100 и более метров при температуре от 1100 до 1300 градусов на протяжении 70-80 часов (3 суток). После того, как ступени и плитка прошли обжиг в туннельной печи – они «разделяются» друг от друга на специальном оборудовании, при этом удаляются технические перемычки (ребра жесткости). Таким образом, две соединенных вместе ступени или плитки отделяются друг от друга и получаются два отдельных элемента. Далее следует упаковка в коробки и на паллеты. После чего материал отправляется покупателям.
Экструдированные керамогранитные ступени и напольная плитка – это материал который производится методом ГОРИЗОНТАЛЬНОЙ экструзии (не путать с методом сухого прессования). ГОРИЗОНТАЛЬНАЯ формовка необходима для того, чтобы уменьшить высоту изделия на конвейерной ленте (чтобы изделия могли поместиться в узкую камеру обжига роликовой печи). В составе «рецепта» экструдированного керамогранита есть в обязательном порядке полевой шпат (это измельченная горная порода), кварцевый песок (могут добавлять а могут и нет) каолиновые глины и различные добавки (пластификаторы, красители). Как правило, «полевой шпат» составляет от 30 до 50% состава рецепта, остальные 50% это кварцевый песок и каолиновые глины (не тугоплавкие!!!).
Полевой шпат производят горно-обогатительные комбинаты в Европе и России. Именно он является основой любого экструдированного керамогранита, и именно от него сам керамогранит и получил свое название «Керамический гранит»: а полевой шпат, это по сути и есть измельченный в порошок гранит, горная порода. Керамогранит может производится методом сухого прессования (на прессе) или методом горизонтальной экструзии (выдавливания) – такой метод изобрели относительно недавно, и он позволяет делать ступень с «литым капиносом» т.е. носик ступени составляет единое целое с плиткой, так же, как и у настоящего клинкера. Технология производства экструдированного керамогранита следующая: Сначала подготавливается масса - смешиваются все ингредиенты рецепта (полевой шпат, кварцевый песок, каолин, пластификаторы, красители и т.д.), далее увлажненная керамогранитная масса попадает в экструдер из которого выдавливается горизонтально.
Ступень с литым капиносом выдавливается на специальной подложке, которая соединена со ступенью техническими перемычками (ребрами жесткости) - это придает ступени ровную поверхность для транспортирования по конвейеру, глазуровке и покраске), а напольная плитка выдавливается горизонтально сразу на конвейерную ленту (без подложки, там нет технических перемычек). Далее, происходит обрезка ступеней и плитки под нужный размер специальным резаком (прямо на конвейерной ленте). После этого, заготовки проходят короткий предварительный обжиг или сушку от 30 минут до нескольких часов в сушильной камере (горячий воздух для нее забирается из основной роликовой печи для обжига), далее происходит глазурование и покраска, после чего, заготовки отправляются по конвейеру в роликовую печь (ступени и плитка транспортируются в самой роликовой печи по крутящимся роликам (отсюда и ее название) – где они проходят окончательный обжиг при температуре до 1300 градусов на протяжении 2-3 часов (в зависимости от рецепта массы, обжиг может составлять до 10 часов и более, но как правило он длиться гораздо меньше).
После этого, ступень отделяется от подложки соединенными техническими перемычками (ребрами жесткости), их разъединяют специальные молотки, а просто плитка сразу проходит далее на упаковку т.к. она не соединена с подложкой, а транспортируется по конвейеру в виде готового изделия. Далее изделия упаковываются в коробки на паллеты и отправляются покупателям.
Это вкратце о методе производства настоящего клинкера и экструдированного керамогранита. А теперь давайте разбираться, как это выглядит в жизни и как отличить настоящий клинкер от экструдированного керамогранита. В настоящее время визуально отличить экструдированный керамогранит от настоящего клинкера сложно даже специалисту, не то что обычному покупателю.
Напольная плитка из Клинкера и Экструдированного керамогранита

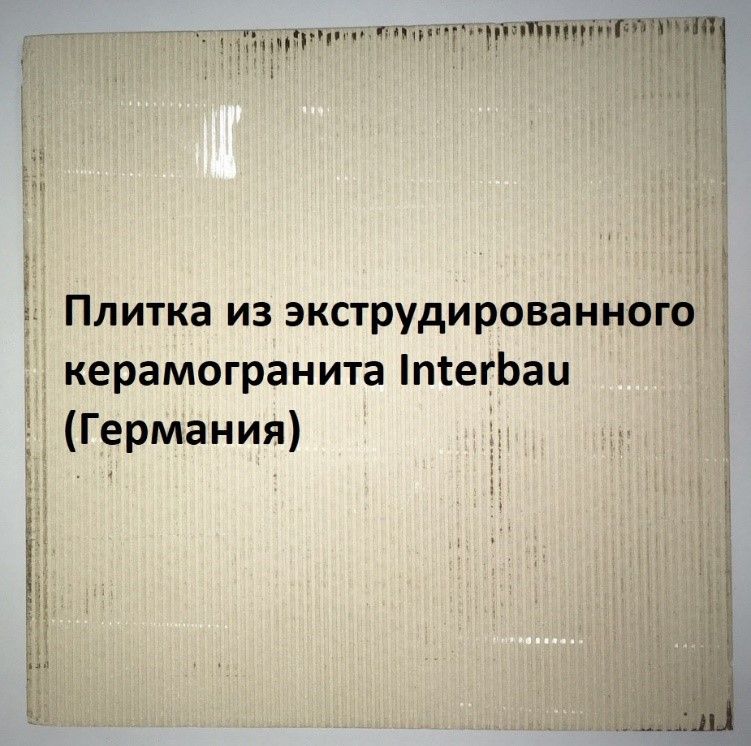
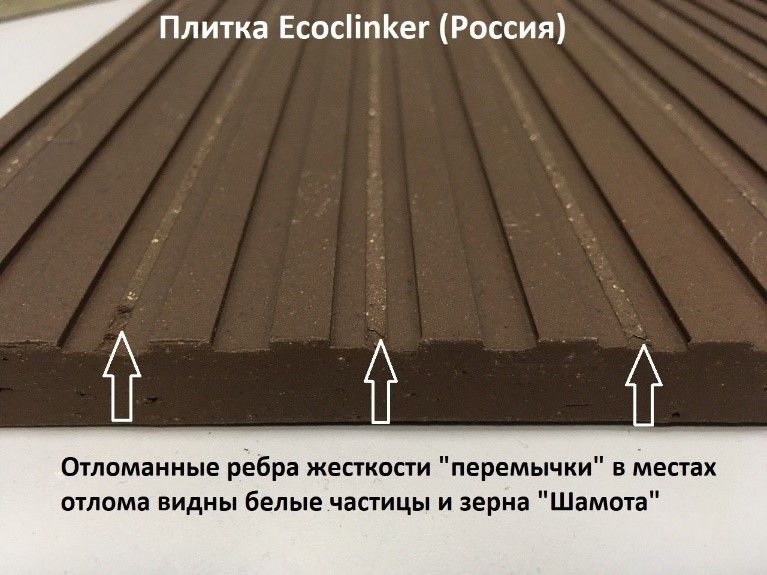
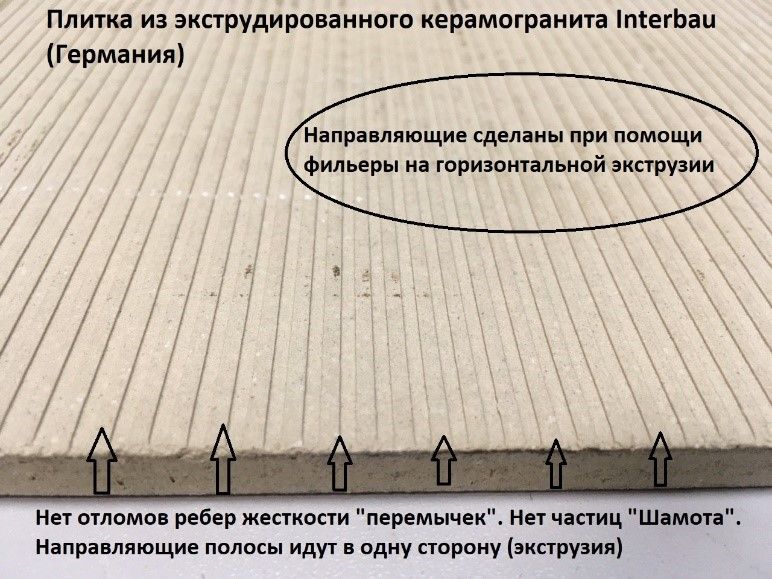
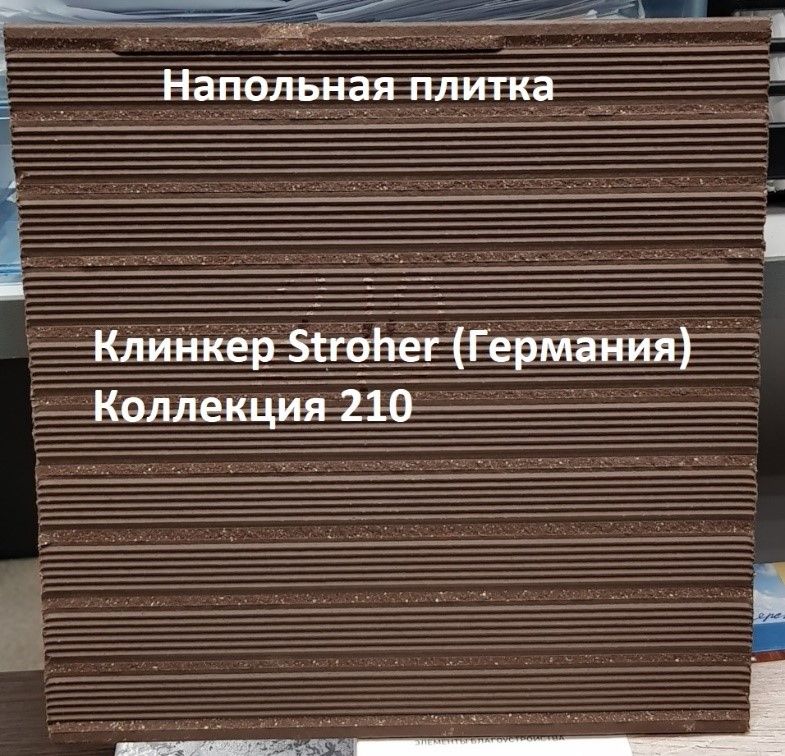
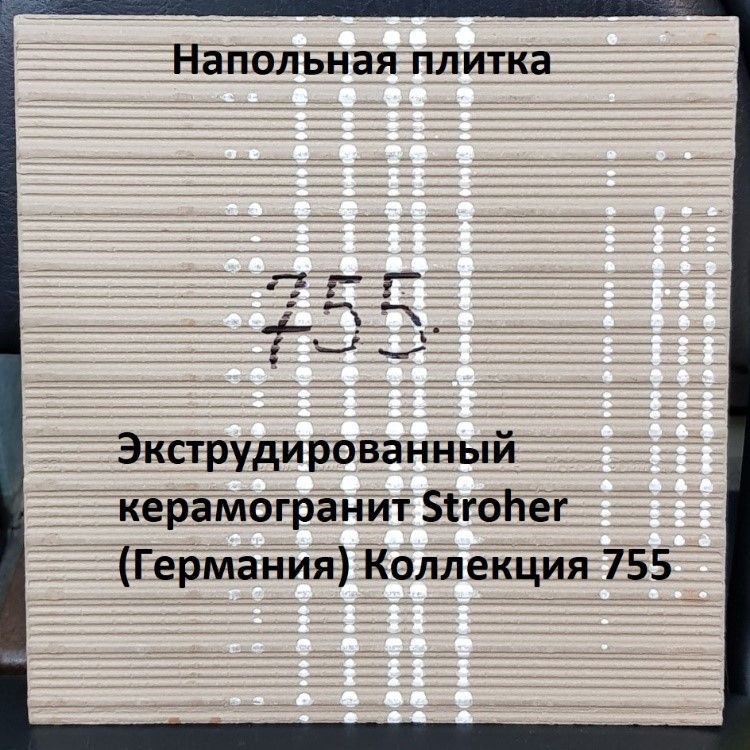

Ступени из клинкера и Экструдированного керамогранита
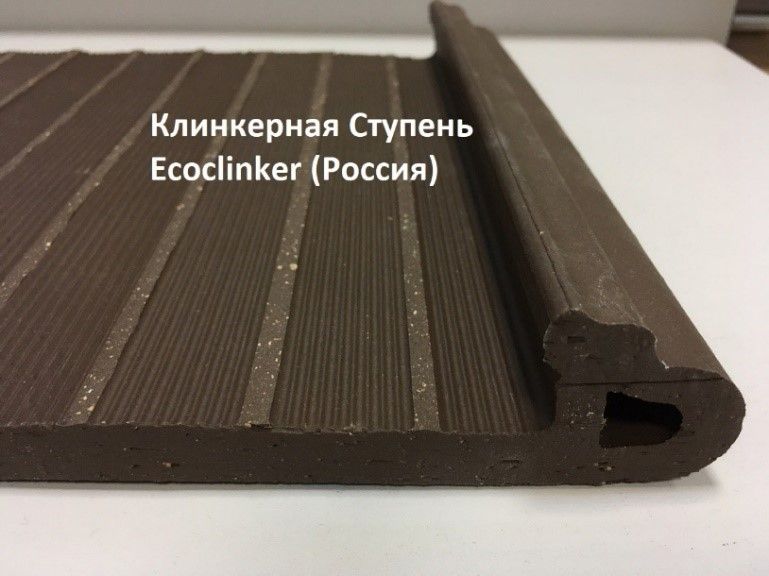
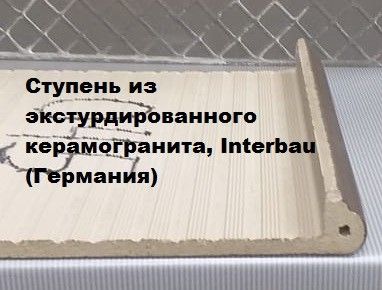
Ступени из клинкера и экструдированного керамогранита: имеют идентичную монтажную (обратную) поверхность. Имеются «отломы» – места где были технические перемычки, соединявшие клинкерные ступени друг с другом или где керамогранитная ступень соединялась с подложкой. Отличить их можно только по следующим параметрам: На месте отлома ребер жесткости «технических перемычек» у настоящей клинкерной ступени и клинкерной плитки выступают частицы «шамота» мелкой фракции белого или темного цветов. В экструдированном керамограните шамота нет.
-
ступени, каталог коллекций Керамогранит.Ру
Керамогранитная ступень, как правило серого цвета (обесцвеченная масса, цвет светлый или цвет цемента-бетона, но некоторые заводы добавляют красители, которые красят керамогранитную массу в темные цвета для того чтобы снизить контраст покрашенной лицевой поверхности и обратной стороны «монтажной поверхности, в некоторых случаях используют полевой шпат или каолин другого цвета, чтобы «затемнить» заготовку). Настоящий клинкер может иметь несколько цветовых вариаций (полная масса коричневая, желтая, кирпичного цвета, как правило это 5-7 натуральных цветов + оттенки или флэш-обжиг) Клинкер - толщина ступеней 12-16 мм. Клинкер - толщина напольной плитки варьируется от 12 до 30 мм. Толщина клинкерной напольной плитки и ступеней никогда не бывает тоньше 12 мм.
В то же время, толщина экструдированной керамогранитной ступени не более 8-10 мм, толщина экструдированной керамогранитной плитки 6-8 мм, очень редко 9 мм. Толщины более 9 мм не бывает. Обычно тонкие изделия из клинкера – это фасадная плитка, которую нельзя использовать в качестве напольной плитки. В этой статье мы ее не рассматриваем.
Напольная плитка из Клинкера и Экструдированного керамогранита: а вот тут отличить легко. Отличия очень заметны. Клинкерная плитка имеет такие же «отломы» перемычек (от ребер жесткости) как и у ступени т.к. экструдер выдавливает настоящий клинкер (плитку) соединенными друг с дружкой при помощи технических перемычек т.е. в одном блоке две ступени или две плитки (см фото выше). А потом, они отделяются друг друга на специальном оборудовании – в результате чего и у ступени и у плитки есть характерные места «отломов технических перемычек» на обратной стороне (монтажной поверхности).
А вот у экструдированной керамогранитной плитки таких отломов от перемычек НЕТ т.к. выдавливание керамогранитной плитки из экструдера идет в одну линию и сразу на конвейер. В 100% случаев экструдированный керамогранит (ступени и плитку) в обязательном порядке глазуруют и красят на специальном покрасочном оборудовании (цифровая печать-покраска или с помощью ротоколора). Вы никогда не встретите ступени из «неглазурованного и некрашенного» экструдированного керамогранита J т.к. цвет некрашенного керамогранита – это цвет обычного бетона или цемента, т.е. он светлый и бесцветный, именно по этой причине ЕГО ВСЕГДА глазуруют и красят т.к. мало какой покупатель захочет покупать себе домой ступени и плитку цвета бетона по цене в десятки раз дороже бетона J А вот настоящий клинкер бывает натуральный неглазурованный и не крашенный (цвет достигается путем смешения друг с другом тугоплавких глин разных сортов) и смотрится он великолепно и очень дорого. Отличаются так же и технические характеристики клинкера и экструдированного керамогранита:
Клинкер: водопоглощение до от 3% до 6%, паропроницаем (можно использовать на стенах домов без вентилируемых фасадов и клеить клинкер напрямую к зданию) Клинкер на много лучше держит ударные нагрузки чем керамогранит. Случаи сколов не заметны т.к. поверхность снаружи и внутри - одного цвета. Отлично подходит для входных групп домов (зоны ступеней, площадки для парковки а/м, крыльцо, дорожки и т.д.) т.к. именно там происходит чистка снега и уборка при помощи «специализированных инструментов в виде лома и лопаты J» и все это сопровождается ударными нагрузками т.к. лед и снег счищают с крыльца отнюдь не при помощи мягкой швабры или пылесоса J
Экструдированный керамогранит: водопоглощение от 0,5 до 3%, Не паропроницаем (по этому использовать экструдированный керамогранит на стенах домов можно ТОЛЬКО на системах с вентилируемыми фасадами). За счет того, что экструдированный керамогранит в процессе обжига в роликовой печи «остекловывается» и не имеет в своем составе тугоплавких глин – он более хрупкий чем настоящий клинкер. Очень боится ударных нагрузок (лопатой, ломом, падения на них любых предметов, особенно металлических).
Весь экструдированный керамогранит глазурован и покрашен, а значит, в лучшем случае что произойдет – это отколется кусок глазуровки и краски (пострадает эстетический внешний вид, оголится внутренняя часть плитки цвета бетона или цемента) а в худшем – плитка или ступень просто треснут и разобьются. При монтаже необходимо использовать не только специальный уличный клей для керамогранита, но и специальным образом подготовленное армированное основание!! т.к. адгезия к клею у экструдированного керамогранита очень плохая (необходимы специализированные клея которые на молекулярном уровне при помощи химической реакции соединят бетонное основание с керамогранитом).
Вы можете сами провести данный эксперимент. Он показывает, что есть настоящий клинкер, а что есть экструдированный керамогранит……Для этого достаточно расположить рядом интересующие Вас ступени и плитку и по очереди кидать на них с одинаковой высоты любой предмет, можно начинать с высоты 50 см (шарик от подшипника, столовый нож тупым закругленным концом «тыльником», все что найдете под рукой…).
Производители:
Настоящий клинкер производят в Германии, Испании, Польше и России. Отличный по качеству настоящий клинкер делают Немецкие заводы Stroher, Interbau, ABC. Хороший клинкер делают Испанские заводы: Gres de Aragon, Gresmanc, Gres de Breda. В Польше клинкер методом вертикальной экструзии делает только завод King Klinker (ступени и плитка таких Польских заводов как Paradiz, Opocno, Tubadzin и т.д. - не имеют ничего общего с клинкером, материал этих заводов делается методом сухого прессования с последующим обжигом в роликовой печи, состав рецептов неизвестен, но это не керамогранит и не клинкер). В России, единственный завод, который производит клинкерные ступени и напольную плитку это Ecoclinker.
Экструдированный керамогранит производят Stroher, Interbau, Gres de Aragon, Exagres и многие другие заводы Испании и Германии. Практически все заводы переориентировали свои производства на выпуск этой продукции, т.к. эта технология дешевле в себестоимости и производительность по сравнению с клинкерным производством выше от 20 до 40 раз. Представьте себе, что за одинаковый промежуток времени можно произвести 1000 м2 клинкера или 30000 м2 экструдированного керамогранита !! Что заводу выгоднее делать….? J В России пока не производят керамогранит методом горизонтальной экструзии. У нас делают керамогранит методом сухого прессования – такая технология для производства напольной плитки гораздо лучше, чем методом экструзии (т.к. пресс под высоким давлением гораздо качественнее и плотнее делает заготовку) но методом сухого прессования невозможно сделать фронтальную ступень с «литым капиносом», по этому, все ступени отечественных керамогранитных плиточных заводов (Керама Марацци, Эстима, Италон, и т.д.) делаются с клееными капиносами или производятся путем нарезки «насечек» на обычной плитке или они и вовсе не имеют в своем ассортименте фронтальных ступеней, а продают только напольную или настенную плитку.
Клинкер или керамогранит что лучше
Итог: Если материал отформован методом вертикальной экструзии-высушен в сушильных камерах и обожжен в туннельной печи – это КЛИНКЕР. Если материал отформован методом горизонтальной экструзии-обожжен в роликовой печи – это НЕ КЛИНКЕР. Настоящий клинкер невозможно обжечь в роликовой печи – а экструдированную керамогранитную массу невозможно обжечь в туннельной печи.
Итак, подведем итог: если вы выбираете себе материал для облицовки крыльца, ступеней, площадки под автомобиль, зоны мангала или барбекю, то вам в равной степени неплохо подойдут оба вида рассматриваемого нами материала. Но настоящий клинкер, в любом случае, будет иметь преимущество как более прочный, практичный и более долговечный материал.
Экструдированный керамогранит порадует своих покупателей обилием всевозможных рисунков и расцветок. Радовать правда будет не долго, т.к. при неаккуратном использовании он склонен к разрушению глазуровки и покраски и в конечном итоге потерей эстетики и внешнего вида с последующим ремонтом или замены на настоящий клинкер!
Статья предоставлена производителем клинкерной продукции Экоклинкер (Россия).